Drive shafts are crucial components in a vehicle's drivetrain, responsible for transmitting torque from the engine to the wheels. The choice of materials for drive shafts is essential to ensure strength, durability, and overall performance. The two primary materials used for manufacturing drive shafts are steel and, to a lesser extent, aluminum.
Steel:
Common Alloys: Various steel alloys are used in the construction of drive shafts. Common choices include carbon steel, alloy steel, and high-strength steel alloys.
Advantages:
Strength: Steel is known for its high tensile strength, making it capable of withstanding the torque and rotational forces encountered in drive shaft applications.
Durability: Steel drive shafts exhibit excellent durability and resistance to deformation, making them suitable for heavy-duty and high-performance vehicles.
Cost-Effective: Steel is generally more cost-effective than certain alternative materials, contributing to its widespread use.
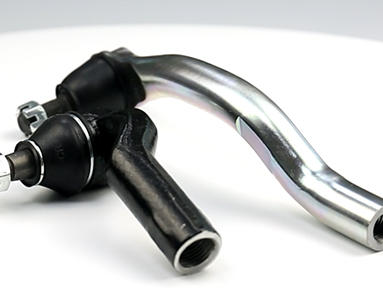
Aluminum:
Aluminum Alloys: Some drive shafts, particularly in lightweight and high-performance applications, are made from aluminum alloys. Common alloys include 6061 and 7075.
Advantages:
Weight Reduction: Aluminum is significantly lighter than steel, contributing to weight reduction in the vehicle. This can be particularly advantageous for improving fuel efficiency and overall performance.
Corrosion Resistance: Aluminum exhibits natural corrosion resistance, reducing the risk of rust and corrosion compared to steel.
High Strength-to-Weight Ratio: Aluminum alloys offer a high strength-to-weight ratio, providing adequate strength while keeping the overall weight lower.
Factors Affecting Material Selection:
Vehicle Type and Application:
The type of vehicle and its intended use play a crucial role in material selection. Heavy-duty trucks and off-road vehicles often use steel for its strength, while lightweight and high-performance vehicles may opt for aluminum for its weight-saving benefits.
Torque and Power Requirements:
Vehicles with higher torque and power requirements, such as trucks and performance cars, may lean towards steel drive shafts to handle the increased stress.
Cost Considerations:
Cost is a significant factor in material selection. While steel is generally more cost-effective, aluminum's benefits in weight reduction may justify its use in certain applications despite its higher cost.
Weight Considerations:
For applications where minimizing weight is a priority, such as in sports cars or race cars, aluminum drive shafts are preferred due to their lower density.
Corrosion Resistance:
In environments where corrosion is a concern, such as in marine applications, aluminum may be chosen for its inherent corrosion resistance.
Manufacturing Processes:
The manufacturing processes involved in shaping and fabricating the drive shaft may influence material selection. Steel is often more forgiving in certain manufacturing processes.
Cost-Performance Trade-Off:
The choice between steel and aluminum often involves a trade-off between cost and performance. Steel is more cost-effective, while aluminum offers advantages in weight savings and corrosion resistance.